In industries like mining, construction, renewable energy, and agriculture, where the heartbeat of operations is often the rhythmic hum of machinery and equipment, the choice of parts can significantly influence operational efficiency, cost-effectiveness, and long-term viability. A critical decision in this context is the selection between Original Equipment Manufacturer (OEM) parts and aftermarket parts. This choice is not black and white, but rather a nuanced one that demands careful consideration of potential benefits balanced against potential risks.
A Deeper Look into the Benefits of Aftermarket Parts
Cost-Effectiveness: One of the most compelling advantages of aftermarket parts is their affordability compared to OEM parts. A study by the Automotive Aftermarket Suppliers Association found that aftermarket parts are, on average, 29% cheaper than their OEM counterparts. For businesses managing vast fleets of machinery, these savings can accumulate to a substantial amount, making a significant impact on the overall operational budget. The cost-effectiveness of aftermarket parts also allows for greater flexibility in managing resources, with the savings potentially being redirected to other areas of need within the operations.
Availability and Variety: Aftermarket manufacturers are known for offering an extensive range of options, often surpassing the variety provided by OEMs. This can be particularly beneficial for operators of older equipment or less common models, where OEM parts may be difficult to source or have been discontinued. The wider variety also offers operators the flexibility to select parts based on their specific needs and budget constraints, rather than being limited to the options provided by the OEM. Furthermore, the widespread availability of aftermarket parts can help minimize downtime by ensuring that necessary parts are readily accessible when needed.
Innovation: The aftermarket parts industry is a hotbed of innovation, with many manufacturers focusing on enhancing and improving upon original designs. These aftermarket parts may offer superior performance, durability, or efficiency compared to their OEM equivalents. Manufacturers are able to leverage advancements in material science, manufacturing techniques, and design methodologies, combined with real-world feedback from operators, to engineer parts that meet or exceed the capabilities of OEM parts. According to a report by Frost & Sullivan, around 35% of aftermarket parts offer some form of improved performance or durability feature.
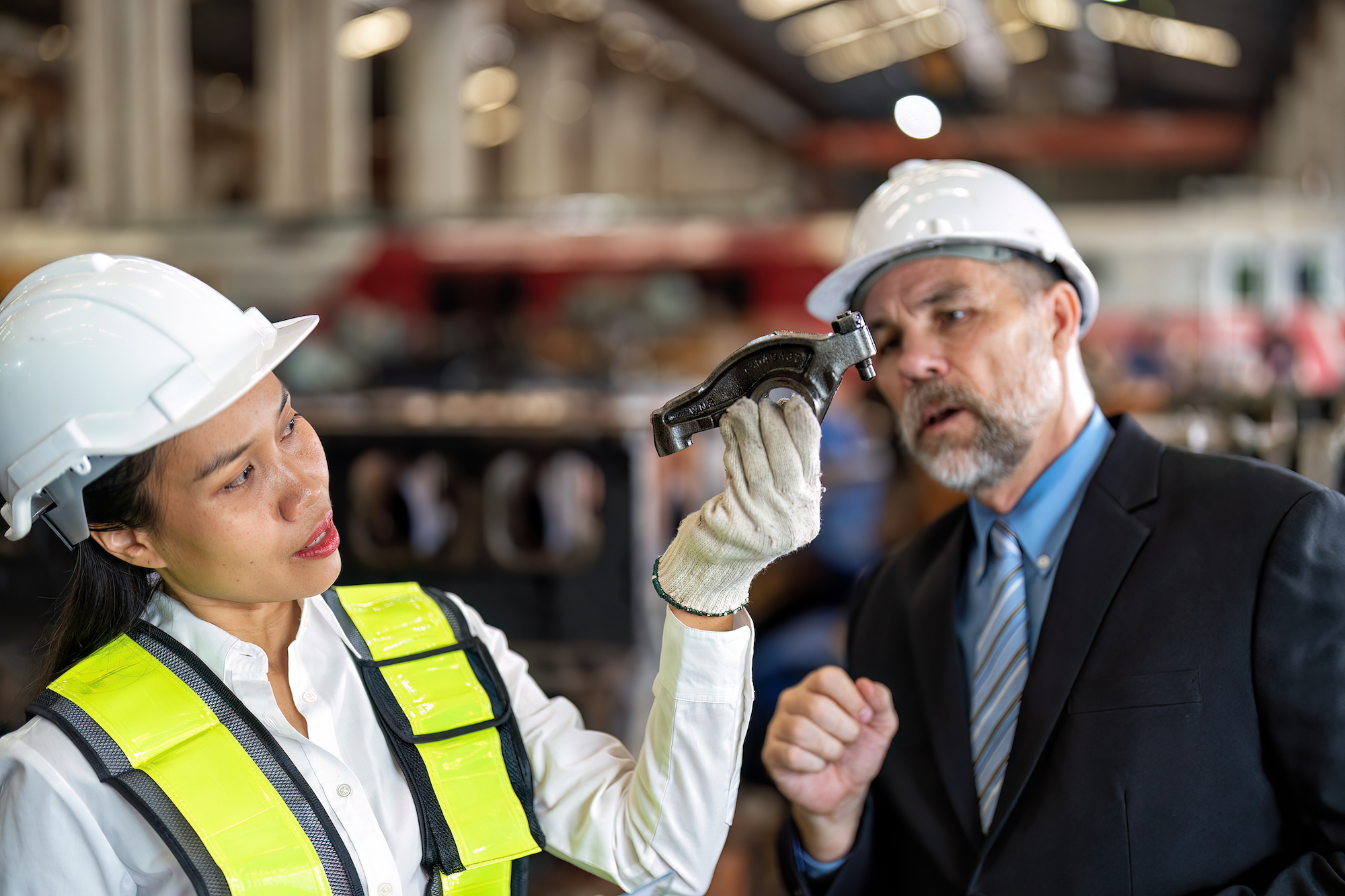
The Other Side of the Coin: Risks of Aftermarket Parts
While the advantages of aftermarket parts are significant, it's essential to consider the potential risks associated with their use.
Quality Concerns: The quality of aftermarket parts can vary dramatically, with some parts matching or exceeding OEM quality, while others fall short. Lower-quality parts can lead to a range of issues, from reduced performance and increased maintenance requirements to potential safety risks. In a survey conducted by the Original Equipment Suppliers Association, 37% of respondents cited quality concerns as one of the primary challenges associated with aftermarket parts.
Compatibility Issues: Even if an aftermarket part is of high quality, it may not fit or function properly with the existing equipment. This could lead to inefficiencies, increased wear on other parts, or even equipment failure. A study published in the Journal of Operations Management found that compatibility issues with aftermarket parts could increase equipment downtime by up to 15%, significantly impacting productivity and operational efficiency.
Warranty Considerations: Warranties are another critical factor to consider when deciding between OEM and aftermarket parts. Aftermarket parts often come with shorter warranties, which could result in higher costs if the part fails prematurely. Moreover, using aftermarket parts could potentially void the warranty of the equipment